What is LBS
LBS optical machine is an optical projection equipment based on laser beam scanning. Its full name is Laser Beam Scanning, which literally means "laser beam scanning". To put it simply, the LBS optical machine uses MEMS galvanometers to precisely control the reflection direction of the light source laser beam, so that each laser beam is reflected to a specific position and a single pixel is formed on the imaging medium.[1]. Because the MEMS galvanometer is very fast, the LBS optical machine can satisfy the visual persistence effect of the human eye, quickly dot the imaging medium, and finally form an image that can be perceived by the human eye.[1]。
Persistence effect of human vision
figure 1).Example of revolving lantern
LBS imaging mechanism
Figure(2).The working principle of MEMS galvanometer
When LBS works, the RGB laser will first generate three laser beams: red, green, and blue. The laser beams are coupled to the surface of the MEMS galvanometer through the optical system. Secondly, the electronic control system will calculate and control the deflection angle and deflection speed of the MEMS galvanometer based on the information of the image to be displayed, and deflect the laser beam to a specific position, where the beam forms a pixel.[1]。
As shown in Figure (3), after completing the scanning deflection of one pixel, the MEMS galvanometer will repeat the previous steps for the remaining pixels until a complete image is drawn. Although only one independent pixel appears on the imaging surface at a time, combined with the human eye persistence phenomenon mentioned above, the human eye and brain can completely perceive each frame of image from point to surface.[1]。
Figure(3).LBS imaging principle
Advantages of LBS
Small size and flexible usage scenarios
Due to its unique design and structure, LBS has the advantage of compact size. Traditional display technologies (such as DLP) often require the use of multiple lenses and optical elements to focus the image[4], while LBS only requires RGB lasers and one or more compact MEMS galvanometers for scanning imaging. Therefore, compared with other imaging systems, LBS does not require a complex optical system to achieve imaging. Therefore, LBS has a significant advantage in terms of volume (Figure (4)). At the same time, because LBS is scanning imaging, there is no fixed imaging focal length, and it is more capable of clear projection on different projection distances and projection surfaces, thus providing higher flexibility in usage scenarios.[4]。
Figure(4).Comparison of LBS and DLP volume structures
Low power consumption
High contrast
Figure(5).LBS, LCD and DLP display effects
色彩表现更佳
Figure(6).Color gamut possible with laser light source (LASER), LED, LCD and CRT displays
Disadvantages of LBS
speckle
Figure (7). Comparison of speckle effects
Distortion
Difficult to achieve high resolution
Color is unstable
Figure (8). Schematic diagram of RGB laser output power changing with temperature
LBS development status
Existing applications
LBS has multiple applications in different fields. In the field of AR and VR, the LBS system can achieve a compact and lightweight design, bringing an immersive visual experience to users; in the field of 3D scanning and imaging, the LBS can generate detailed 3D models of objects or environments, which can be used for industrial design and cultural heritage protection. etc.; in terms of lidar perception, LBS is used to scan and measure distances and create detailed three-dimensional maps of the surrounding environment; in addition, due to higher imaging contrast and better color performance, LBS can also be used in theaters and large outdoor displays[13]。
Vehicle applications
In the automotive field, LBS optical machines can be applied to vehicle HUD (Head Up Display) system, and broaden the HUD technology route in terms of volume and reducing the risk of sunlight intrusion. Due to its small size, LBS can theoretically effectively solve the problem of PGU volume ratio in HUD and achieve a larger field of view (FOV) with the same volume. At the same time, since LBS is a projection technology, it requires a diffusion film for primary imaging, which means that the high-energy-density solar radiation from the outside gathered by the HUD optical system will not be loaded onto the optical machine body, thereby reducing the risk of sunlight intrusion.[14]. However, there are still many problems that need to be solved for vehicle-mounted LBS technology, such as cost, temperature drift, vibration, speckle and other characteristic issues, as well as comprehensive certification of reliability for vehicle regulations. Therefore, the relevant solutions have not yet been implemented in mass production. Therefore, it is a challenge for LBS to mass-produce vehicles without taking too many additional measures while maintaining costs.
In summary, the structural composition and laser characteristics of LBS give it different advantages in imaging and other aspects, but also lead to its high difficulty and high requirements in HUD applications. Understanding the detailed principles of LBS will help to better evaluate and optimize its impact on imaging quality and application in actual scenarios.
#参考来源:
[2]Anderson J, Anderson B. (1993). "The myth of persistence of vision revisited." Journal of Film and Video, 3-12.
[3]Wang, Dingkang, Connor Watkins, and Huikai Xie. (2020). "MEMS mirrors for LiDAR: A review." Micromachines 11(5): 456.
[4]LI Zhao, YUAN Weizheng, WU Meng, et al. (2011). "Micro scanning mirrors with laser diode for pattern generation." Acta Photonica Sinica, 40(11): 1625-1629.
[5]Hofmann, Ulrich, Joachim Janes, and Hans-Joachim Quenzer. (2012). "High-Q MEMS resonators for laser beam scanning displays." Micromachines 3.2: 509-528.[6]Niesten, Maarten, Randy Sprague, and Josh Miller. (2008). "Scanning laser beam displays." Photonics in Multimedia II. Vol. 7001.
[7]Tsai, Pei-Shan, et al. (2009). "Image enhancement for backlight-scaled TFT-LCD displays." IEEE Transactions on Circuits and Systems for Video Technology 19.4: 574-583.
[8]Briers, David, et al. (2013). "Laser speckle contrast imaging: theoretical and practical limitations." Journal of biomedical optics 18.6: 066018-066018.
[9]Akram, M. Nadeem, and Xuyuan Chen. (2016). "Speckle reduction methods in laser-based picture projectors." Optical Review 23.1: 108-120.
[10]Dai, K., and Louie Shaw. (2002). "Distortion minimization of laser‐processed components through control of laser scanning patterns." Rapid Prototyping Journal 8.5: 270-276.
[11]Okamoto, Yuki, et al. (2018). "High-uniformity centimeter-wide Si etching method for MEMS devices with large opening elements." Japanese Journal of Applied Physics 57.4S: 04FC03.
[12]Kumano, Tetsuya, et al. (2016). "Ultracompact RGB Laser Module Operating at+ 85 C." SEI technical review 82.
[13]Merlemis, Nikolaos, Anastasios L. Kesidis, etc. (2020). "Measurement of laser beam spatial profile by laser scanning." European Journal of Physics 42.1: 015304.
[14]McDonald, T. Gus, and Pierre Mermillod. (2023). "Speckle mitigation techniques for laser point scanned displays in head-up display applications." Advances in Display Technologies XIII. Vol. 12443.
The original article was first published on the WeChat official account (Aibang VR Industry News):AR/VR display solution: LBS optical-mechanical technology principle
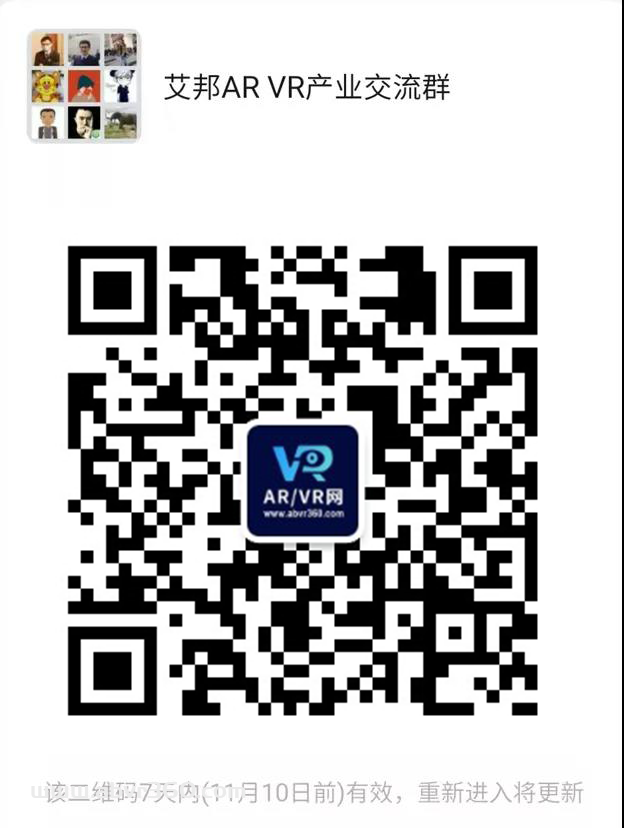